丁腈橡胶可塑度小,韧性大,塑炼时生热大。开炼时要采用低温40℃以下、小辊距、低容量以及分段塑炼,这样可以收到较好的效果。
挤出机构造 、挤出机构造
1 单螺杆挤出机结构示意图 1-电动机; 2-减速装置; 3-冷却水入口;4-冷却水夹套; 5-料斗;6-温度计; 7-加热套; 8-螺杆; 9-滤网; 10-多孔板; 11-机头和口模; 12-机座 (1)传动装置: 由电动机、 减速机构和轴承等组成, 具有保证挤出过程中螺杆转速恒定、 制品质量的稳定以及保证能够变速作用。 (2)加料装置:无论原料是粒状、粉状和片状,加料装置都采用加料斗,加料斗内应有 切断料流、标定料量和卸除余料等装置。 (3)料筒: 料筒是挤出机的主要装置之一,塑料的混合、塑化和加压过程都在其中进 行。挤压时料筒内的压力可达 55Mpa,工作温度一般为 150~250oC,因此料筒是受压和受 热的容器,通常由高强度、坚韧耐磨和耐腐蚀的合金钢制成。料筒外部设有分区加热和冷却的装置,而且各自附有热电偶和自动仪表等。 (4) 螺杆: 螺杆是挤出机的关键部件,一般螺杆的结构如图 2 所示。 (5)口模和机头:机头是口模与料件之间的过渡部分,其长度和形状随所用塑料的种类、制品的形状加热方法及挤出机的大小和类型而定。 机头和口模结构的好坏, 对制品的产量和
质量影响很大,其尺寸根据流变学和实践经验确定。(6)冷却装置:使熔融物料冷却为固体(或产品) ,以便于切割成粒或产品。 (7)卷取(切割): (8)后处理:喷涂、丝印、表面处理等
5、挤出机参数: 、挤出机参数:
(1)螺杆直径(DS) :螺杆外径,常用 60~150mm,直径增大,挤出机输送能力增大,生 产能力提高。 (2)螺杆长径比 L/DS:工作部分的有效长度与直径之比,通常为 20~40,长径比大,混合 均匀,减少逆流和漏流。要求塑化时间长,如硬质塑料、粉状塑料或结晶塑料,长径比要求 较大。热敏性塑料,受热易分解,长径比较小。 (3) 螺槽深度 H:H 小时,产生较高剪切力,有利于塑化,但挤出生产率降低。H 较大, 则反之。H 沿着螺杆轴向变化。 (4)螺旋角θ:螺纹与螺杆横截面之间夹角,θ增大,生产能力提高,剪切作用减小。介 于 10~30 度之间。 (5)螺纹棱部宽 E:太小则漏流增加,产量降低;太大则易局部过热。0.08~0.12 DS。 (6)螺杆与料筒间隙:大小影响挤出机生产能力和塑化效果。较大时,剪切力变小、生产 能力下降、物料熔融塑化慢。密炼机混炼的胶料质量好坏,除了加料顺序外,主要取决于混炼温度、装料容量、转子转速、混炼时间、上顶拴压力和转子的类型等。1、装料容量 即混炼容量,容量不足会降低对胶料的剪切作用和捏炼作用,甚至出现胶料打滑和转子空转现象,导致混炼效果不良。反之,容量过大,胶料翻转困难,使上顶拴位置不当,使一部分胶料在加料口颈处发生滞留,从而使胶料混合不均匀,混炼时间长,并容易导致设备超负荷,能耗大。因此,混炼容量应适当,通常取密闭室总有效容积的60%~70%为宜。密炼机混炼时装料容量可用下列经验公式计算: Q——装料容量,Kg; K——填充稀疏,通常取0.6~07; V——密闭室的总有效容积,L; ρ——胶料的密度,g/cm3。 填充系数K的选取与确定应根据生胶种类和配方特点,设备特征与磨损程度、上顶拴压力来确定。NR及含胶率高的配方,K应适当加大;合成胶及含胶率低的配方,K应适当减小;磨损程度大的旧设备,K应加大;新设备要小些;啮合型转子密炼机的K应小于剪切型转子密炼机;上顶拴压力增大,K也应相应增大。另外逆混法的K必须尽可能大。2、加料顺序 密炼机混炼中,生胶、炭黑和液体软化剂的投加顺序与混炼时间特别重要,一般都是生胶先加,再加炭黑,混炼至炭黑在胶料中基本分散后再加入液体软化剂,这样有利于混炼,提高混炼效果,缩短混炼时间。
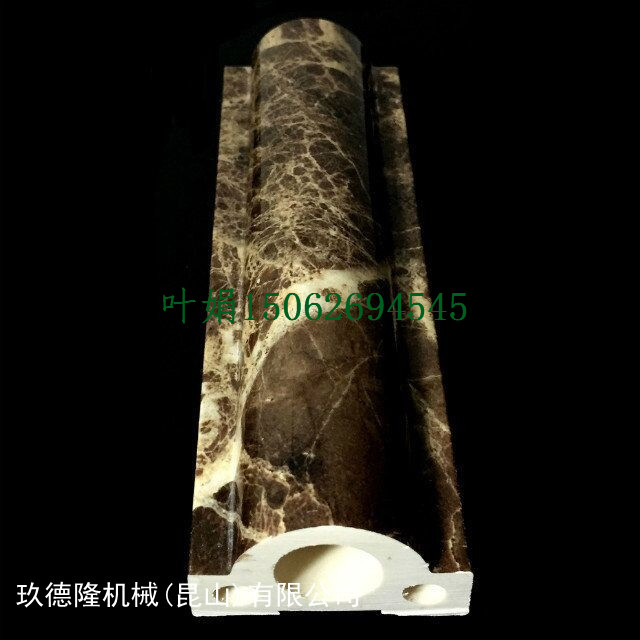
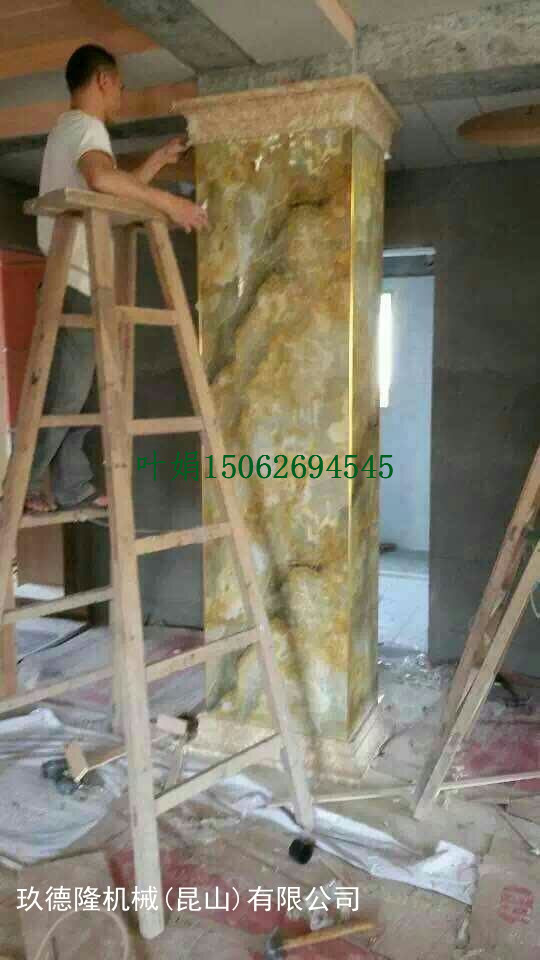
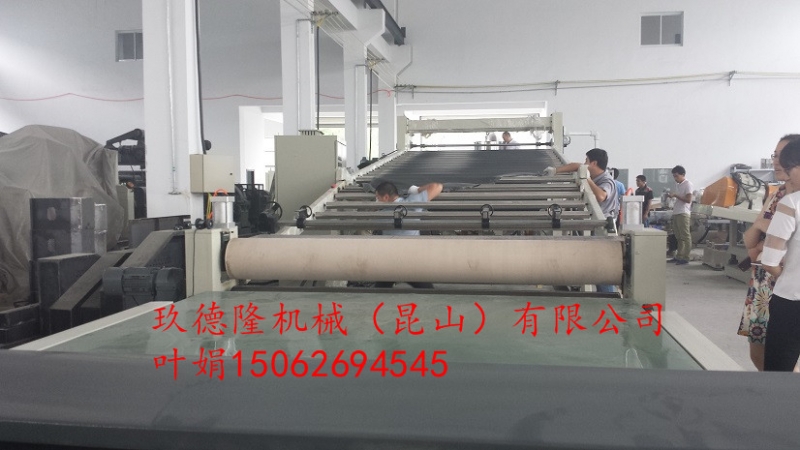